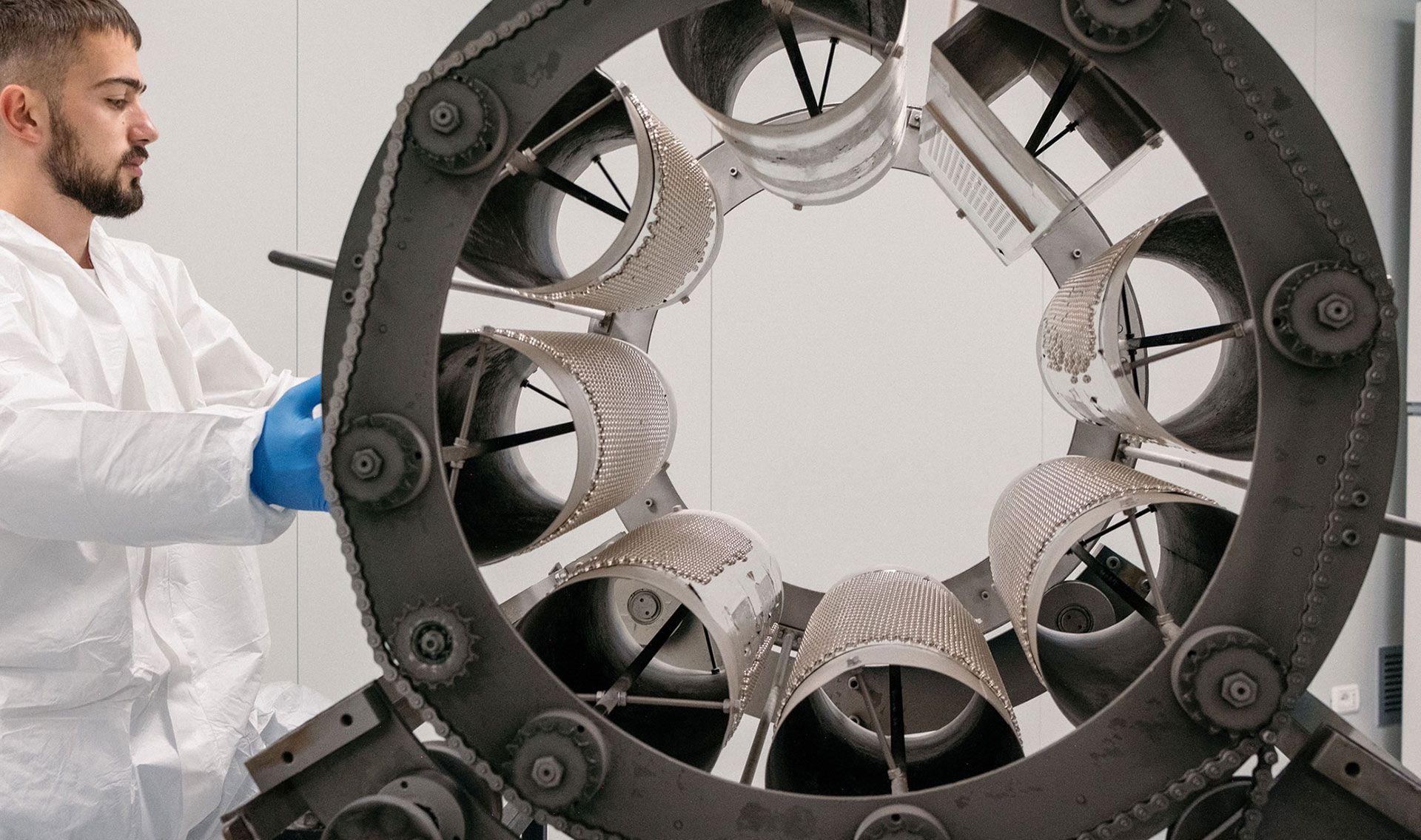
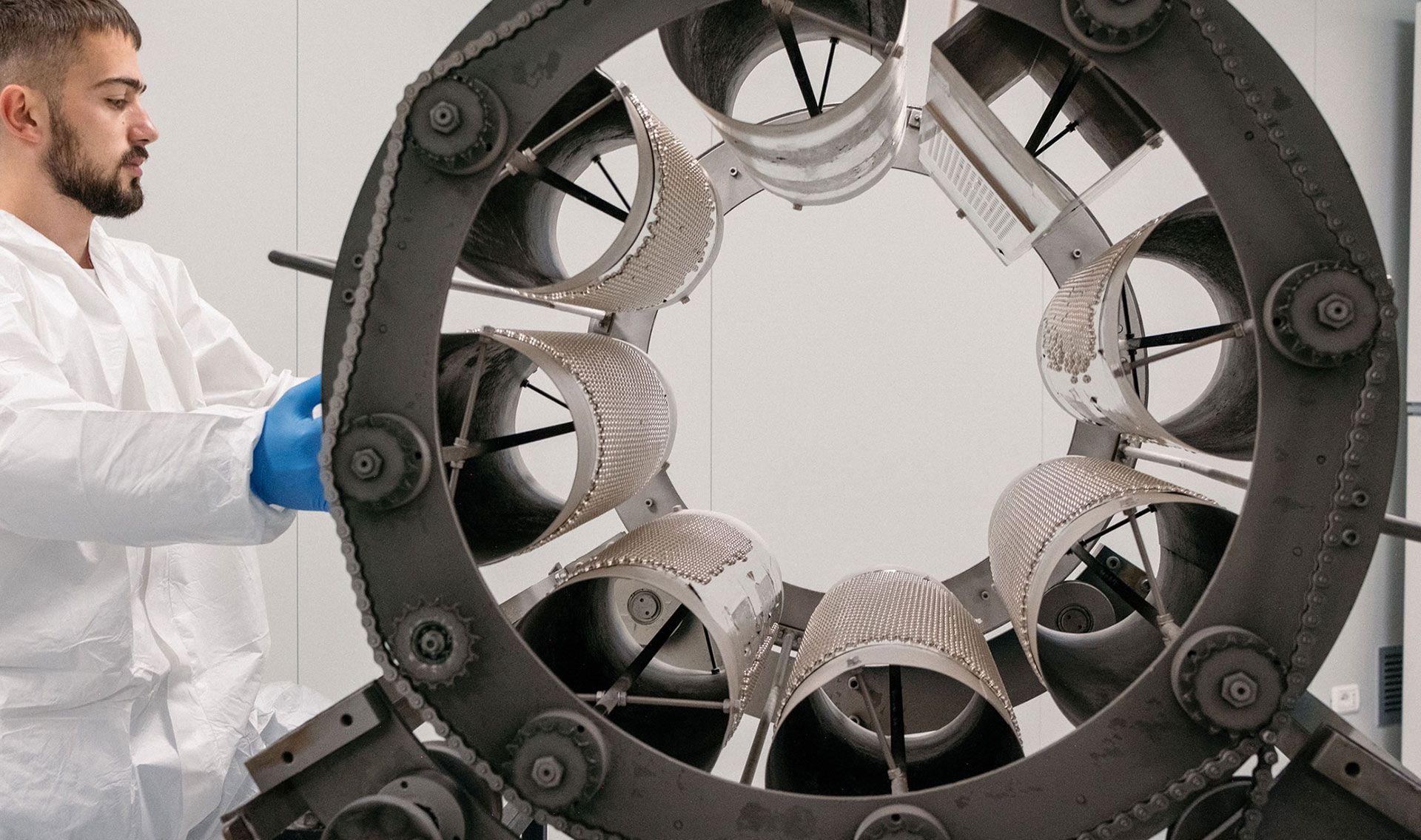
PHYSICAL VAPOR DEPOSITION
That is, physical deposition from vapor phase. Through different evaporation technologies, from thermal/metallization evaporation, magnetron sputtering evaporation, to cathodic arc evaporation, Made Black is able to evaporate metals to obtain both highly aesthetic results and exceptional durability of coatings.
Often considered the most "ecological" coating, as it is carried out completely without the use of water, with PVD is possible to obtain unique metallic colors such as mixcolor / iridescent, gold, metallic blue, absolute black and many others. Made Black today, with 4 production lines, is one of the reference points for this processing in the fashion-luxury sector and not only.
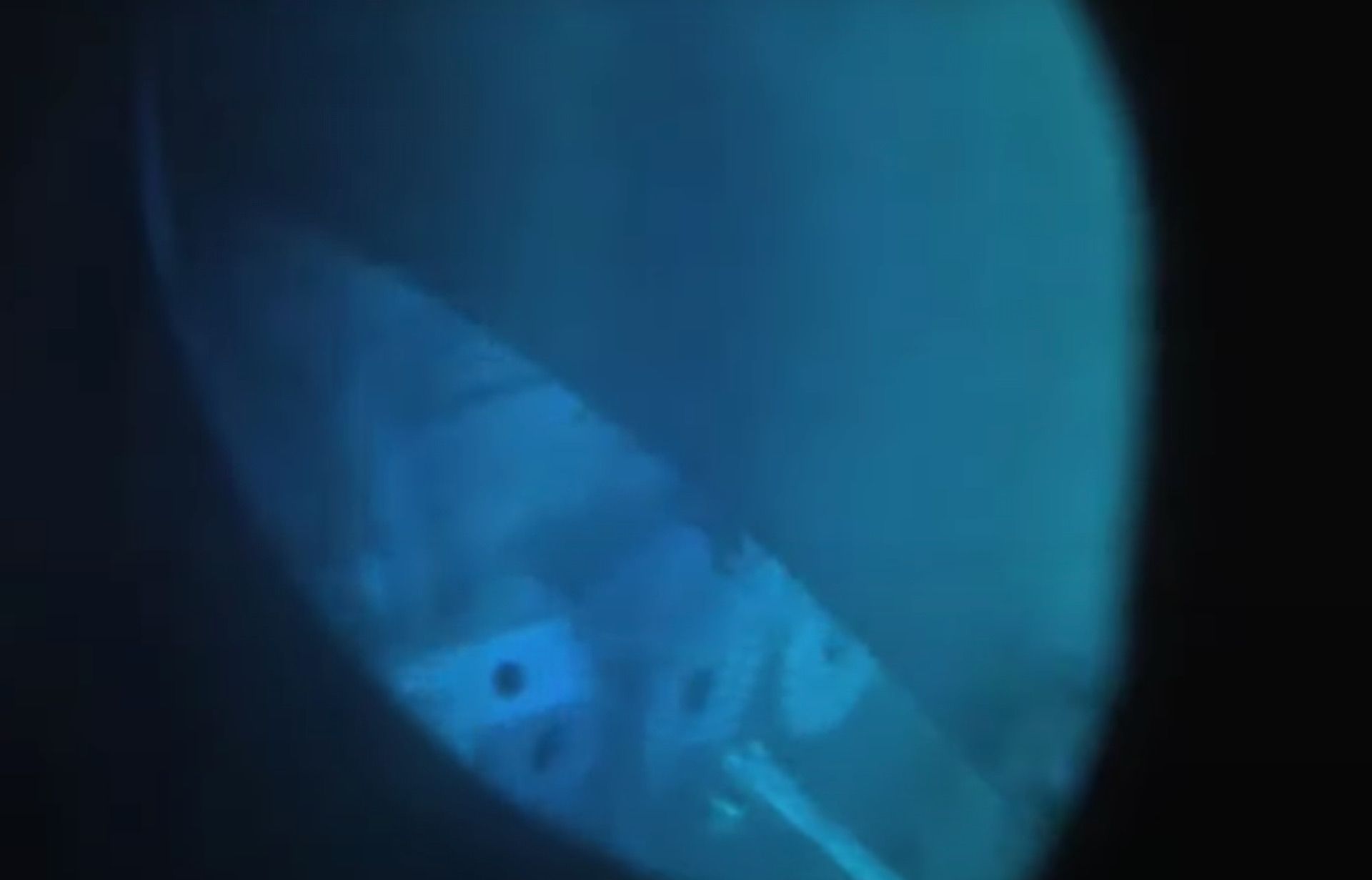
MAGNETRON SPUTTERING
Sputtering PVD is suitable for all materials. It can be used either by direct deposition on already corrosion resistant materials or on any material, even raw materials, in combination with painting, which is used as a base and as a top-coat (with this process, for example, Made Black has introduced the metallization of plastic with a nickel free cycle with very high productivity). Today we can use this technology to deposit a wide variety of metals such as titanium, brass, chrome, silver, 24kt gold and many others.
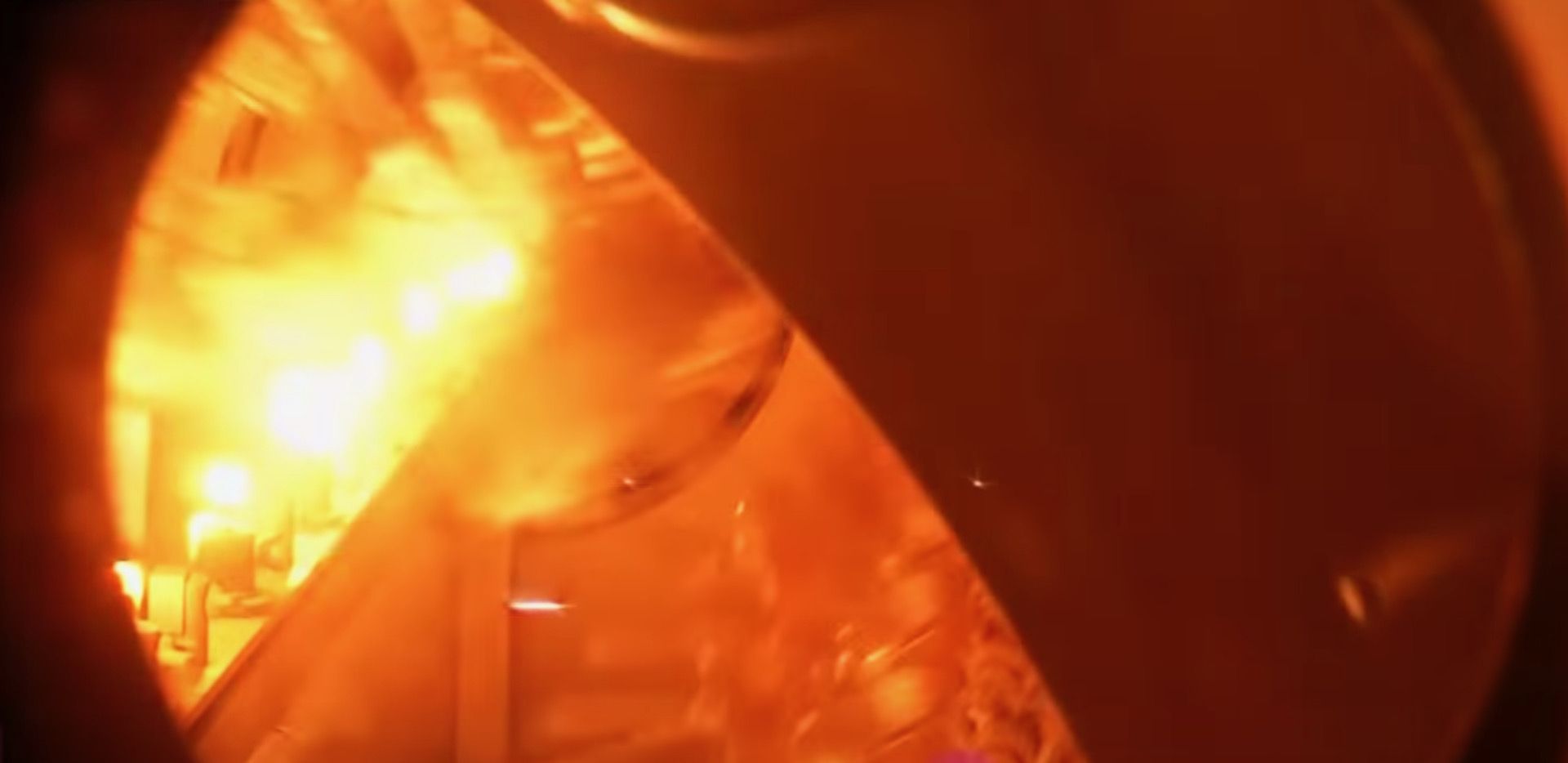
THERMAL EVAPORATION
Thermal evaporation PVD is one of the oldest techniques for the deposition of thin films: the metal is heated to sublimation temperature to evaporate through the action of an electrical resistance. This technique is used today mainly to make very special effects such as iridescent finishes/ aurora borealis.
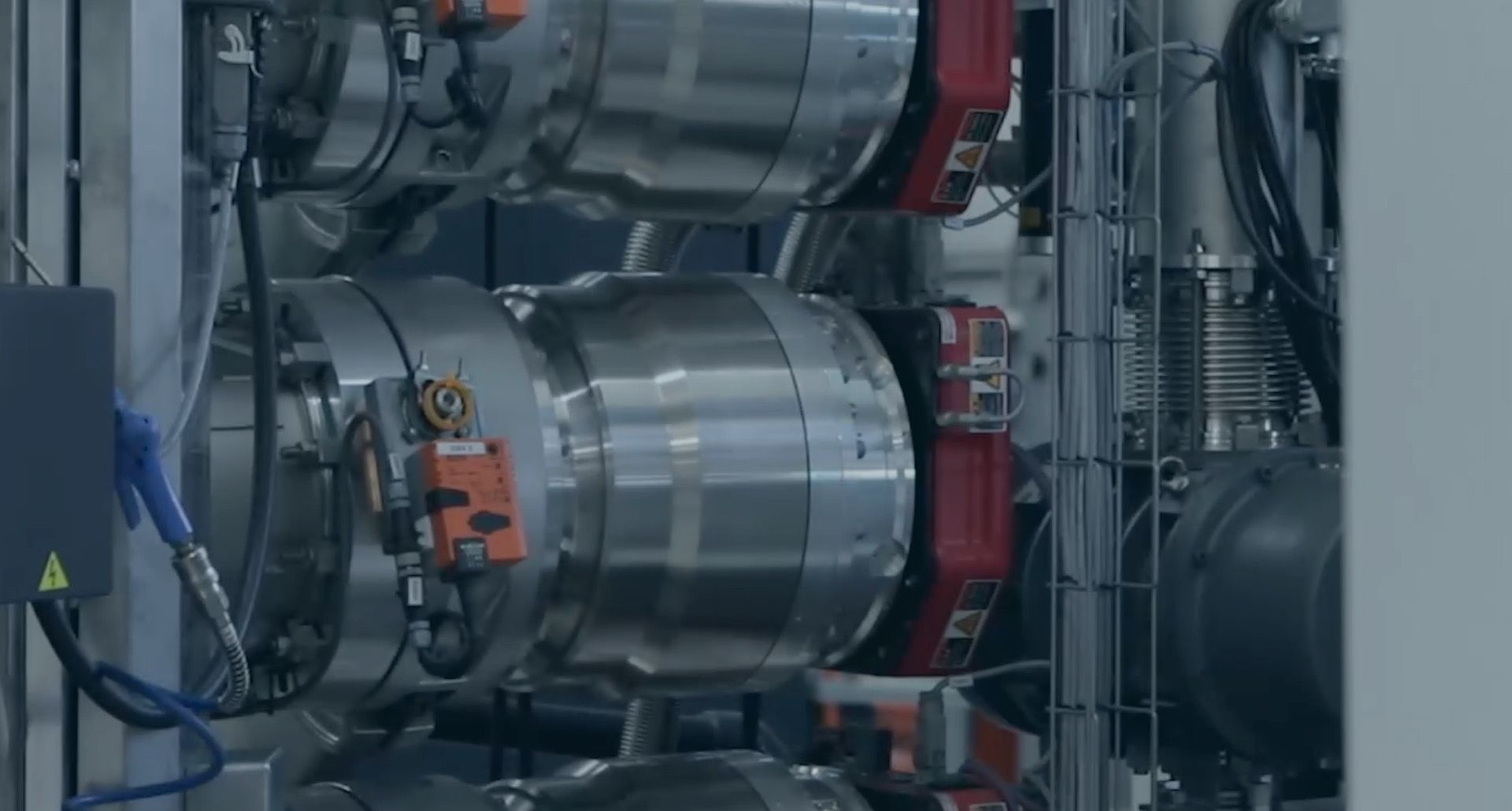
CATHODIC ARC EVAPORATION
The cathodic arc PVD, often used in conjunction with evaporation by magnetron sputtering, is particularly suitable for the coating of corrosion resistant items that need exceptional technical performance.
Through this technology we treat materials such as stainless steel and titanium, as well as brass or pre-galvanized zamak materials, with high performance finishes suitable for highly stressed components such as leather goods feet and carabiners.
With this technique we produce different coatings that by their nature can be defined as technical-decorative such as for example:
- Titanium Nitride (TiN) and Zirconium-Nitride (ZrN), often used together with 24kt gold to make the various shades of gold
- Chrome Carbo-Nitride (CrCN) for black and gunmetal shades
- Titanium Carbo-Nitride (TiCN) to achieve finishes such as bronze/copper effect
- Titanium and chromium oxides (TiOx, CrOx) for iridescent/mix-color effects
Green coatings?
PVD (in particular the one obtained by cathodic arc evaporation) is often considered among the most eco-sustainable coatings as it achieves a practically eternal finish (the so-called "Lifetime finish") and because being deposited under vacuum it does not use potentially polluting water. Nevertheless, it is an energy-intensive process that must be managed with care, find out what we do in Made Black to make it even more sustainable.